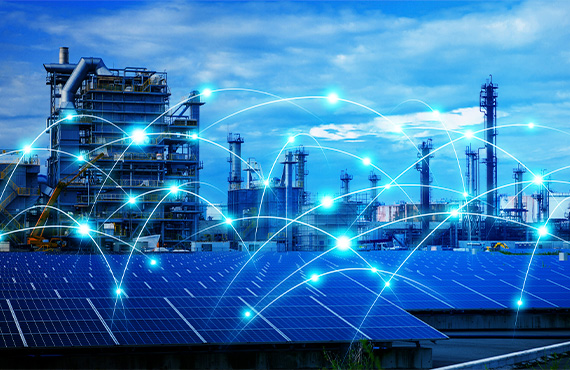
In today's interconnected world, cybersecurity has become a critical concern for manufacturers.
The increasing adoption of digital technologies, such as Industrial Internet of Things (IIoT), cloud computing, and automation, has exposed manufacturing operations to a wide range of cyber threats. Cyber attacks can have devastating consequences, including production disruptions, intellectual property theft, financial losses, and damage to reputation.
Manufacturing facilities are prime targets for cyber criminals due to the high value of their intellectual property, sensitive data, and the potential for physical disruption. A successful cyber attack can lead to operational downtime, compromised product quality, and even safety incidents. The financial implications of such attacks can be severe, with costs associated with lost production, remediation efforts, and potential legal liabilities.
Further, cyber threats are constantly evolving, with attackers employing increasingly sophisticated techniques to exploit vulnerabilities in industrial control systems (ICS) and other manufacturing systems. Ransomware attacks, for instance, have become a significant concern, where cyber criminals hold data or systems hostage until a ransom is paid.
Implementing robust cybersecurity measures is no longer an option but a necessity for manufacturers. By proactively addressing cybersecurity risks, manufacturers can protect their operations, safeguard their data, and maintain the trust of their customers and stakeholders. Failure to prioritize cybersecurity can result in significant financial losses, reputational damage, and regulatory penalties.
Understanding Cyber Threats in Manufacturing
The manufacturing industry faces a wide range of cyber threats that can disrupt operations, compromise sensitive data, and cause significant financial losses. One of the primary threats is malware, which includes viruses, worms, and trojans designed to infect systems and cause damage or steal data. Ransomware, a type of malware that encrypts files and demands a ransom payment, has become increasingly prevalent and can cripple production lines.
Phishing attacks are another major concern, where cybercriminals attempt to trick employees into revealing login credentials or downloading malicious software through fraudulent emails or websites. These attacks can provide attackers with a foothold into the network, allowing them to move laterally and access sensitive systems.
Insider threats, whether intentional or unintentional, also pose a significant risk. Disgruntled employees or contractors with access to critical systems can cause harm, while careless handling of sensitive information or failure to follow security protocols can lead to data breaches or system vulnerabilities.
Manufacturing companies often rely on industrial control systems (ICS) and supervisory control and data acquisition (SCADA) systems to manage and monitor industrial processes. These systems are increasingly connected to corporate networks and the internet, expanding the attack surface and making them vulnerable to cyber threats. Outdated or unpatched systems can provide entry points for attackers, while poorly configured systems can be exploited to gain unauthorized access or disrupt operations.
Implementing a Cybersecurity Strategy
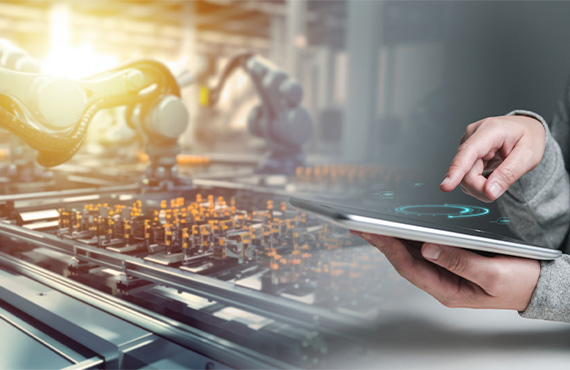
Implementing a robust cybersecurity strategy is crucial for manufacturing organizations to protect their operations, intellectual property, and sensitive data from cyber threats. A comprehensive cybersecurity strategy should encompass several key elements:
- Risk Assessment: Conduct a thorough risk assessment to identify potential vulnerabilities, threats, and their associated impacts on your organization. This assessment should consider both internal and external factors, including legacy systems, third-party vendors, and employee practices.
- Policy Development: Develop and implement clear cybersecurity policies and procedures that outline acceptable use, access controls, incident response protocols, and data protection measures. These policies should be regularly reviewed and updated to align with evolving threats and industry best practices.
- Employee Training: Invest in regular cybersecurity awareness training for all employees, including executives, managers, and front-line workers. Educate them on recognizing and responding to cyber threats, such as phishing attempts, social engineering tactics, and proper handling of sensitive information.
- Access Controls: Implement robust access controls, including multi-factor authentication, least privilege principles, and regular password management practices. Restrict access to critical systems and data to only those who require it for their job functions.
- Patch Management: Establish a rigorous patch management process to ensure that all software, operating systems, and firmware are kept up-to-date with the latest security patches and updates. Unpatched systems can provide entry points for cyber attackers.
- Incident Response Plan: Develop and test an incident response plan that outlines the steps to be taken in the event of a cyber attack or data breach. This plan should include procedures for containment, investigation, recovery, and communication with relevant stakeholders.
- Continuous Monitoring: Implement continuous monitoring and logging mechanisms to detect and respond to potential security incidents in a timely manner. This includes monitoring network traffic, system logs, and user activities for any suspicious or anomalous behavior.
By implementing a comprehensive cybersecurity strategy, manufacturing organizations can proactively address cyber risks, protect their assets, and maintain business continuity in the face of evolving cyber threats.
Securing Industrial Control Systems
Securing industrial control systems (ICS) and operational technology (OT) networks is paramount for manufacturing organizations. These systems are the backbone of production processes, controlling and monitoring critical operations. A cyber attack targeting ICS or OT networks can lead to disastrous consequences, including production downtime, equipment damage, safety incidents, and even environmental disasters.
Manufacturers must adopt a comprehensive cybersecurity approach to protect their ICS and OT environments. This involves implementing robust access controls, network segmentation, continuous monitoring, and incident response protocols. Outdated or unpatched systems can create vulnerabilities that threat actors can exploit, making it essential to maintain a rigorous patch management program and regularly assess system configurations.
Additionally, manufacturers should implement secure remote access solutions, as many ICS and OT systems require remote monitoring and maintenance. Strong authentication mechanisms, encrypted communications, and granular access controls are crucial to mitigating the risks associated with remote access.
Proactive threat hunting and monitoring are also critical components of ICS and OT security. Manufacturers should deploy advanced security solutions, such as intrusion detection and prevention systems (IDS/IPS), security information and event management (SIEM) tools, and anomaly detection systems, to identify and respond to potential threats promptly.
Further, manufacturers must prioritize employee awareness and training programs. Human error and social engineering attacks can compromise even the most robust security measures. By educating employees on cybersecurity best practices, manufacturers can significantly reduce the risk of insider threats and inadvertent security breaches.
Securing ICS and OT networks is a complex undertaking, but it is essential for protecting manufacturing operations, safeguarding intellectual property, and ensuring regulatory compliance. By implementing a comprehensive cybersecurity strategy tailored to their unique requirements, manufacturers can mitigate cyber risks and maintain the integrity and resilience of their critical systems.
Network Segmentation and Monitoring
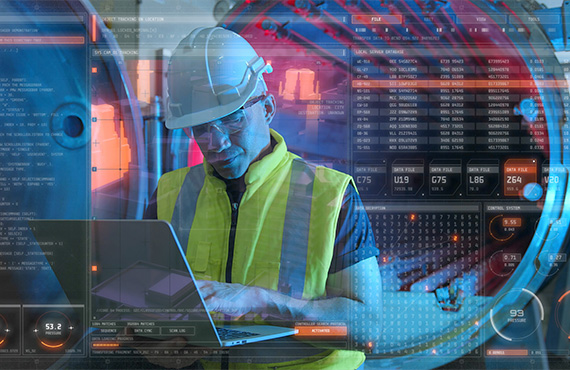
Implementing robust network segmentation and continuous monitoring strategies is crucial for safeguarding manufacturing environments against cyber threats. By dividing your network into smaller, isolated segments, you can effectively limit the potential spread of malicious activities and contain any security breaches within a specific zone.
Network segmentation involves creating logical boundaries within your network architecture, separating critical systems and assets from less sensitive areas. This approach minimizes the attack surface and reduces the risk of lateral movement by threat actors. By strategically segmenting your network, you can enforce granular access controls, ensuring that only authorized personnel and systems can communicate within and across designated segments.
Plus, continuous monitoring plays a vital role in detecting and responding to cyber threats in real-time. Advanced monitoring solutions enable you to establish baselines for normal network behavior, identify anomalies, and promptly investigate and mitigate any suspicious activities. By continuously monitoring your network traffic, system logs, and security events, you can gain valuable insights into potential vulnerabilities, unauthorized access attempts, and ongoing attacks.
Implementing network segmentation and monitoring strategies offers several benefits for manufacturing environments:
- Reduced Risk of Lateral Movement: By isolating critical systems and assets, you can prevent threat actors from moving laterally across your network, minimizing the potential impact of a successful breach.
- Enhanced Access Control: Network segmentation allows you to implement granular access controls, ensuring that only authorized personnel and systems can access specific network segments, reducing the risk of unauthorized access and data exfiltration.
- Improved Incident Response: In the event of a security incident, network segmentation and monitoring facilitate faster incident detection, containment, and response, minimizing the potential damage and downtime.
- Regulatory Compliance: Many industry regulations and standards, such as NIST SP 800-171 and IEC 62443, mandate the implementation of network segmentation and monitoring controls, helping you achieve and maintain compliance.
- Operational Resilience: By isolating critical manufacturing systems and processes, you can maintain operational continuity even in the face of cyber attacks or network disruptions, ensuring uninterrupted production and minimizing financial losses.
To effectively implement network segmentation and monitoring strategies, it is essential to collaborate with experienced cybersecurity professionals who understand the unique requirements and challenges of manufacturing environments. Proconex offers comprehensive cybersecurity solutions tailored to the manufacturing industry, leveraging best practices and industry-leading technologies to protect your critical assets and operations.
Incident Response and Recovery
Effective incident response and recovery measures are crucial for manufacturing organizations to minimize the impact of cyber incidents and ensure business continuity. In today's interconnected world, cyber threats can strike at any time, and having a well-defined incident response plan in place can mean the difference between a minor hiccup and a catastrophic event.
An incident response plan outlines the steps to be taken when a cybersecurity incident occurs, such as a malware infection, data breach, or system compromise. This plan should cover the entire lifecycle of an incident, from detection and analysis to containment, eradication, and recovery.
The first step in an effective incident response is rapid detection and analysis. By implementing robust monitoring and alerting systems, organizations can quickly identify potential threats and initiate the appropriate response procedures. This may involve isolating affected systems, gathering forensic evidence, and engaging cybersecurity experts to assess the extent of the incident.
Once the incident has been contained, the next step is eradication, which involves removing the root cause of the incident and ensuring that all traces of the threat have been eliminated. This may involve patching vulnerabilities, updating software, or implementing additional security controls.
Recovery is the final stage of the incident response process, where organizations restore their systems and data to a known good state. This may involve restoring from backups, rebuilding systems from scratch, or implementing new security measures to prevent similar incidents from occurring in the future.
Having a comprehensive incident response and recovery plan in place not only helps organizations respond effectively to cyber incidents but also demonstrates a commitment to cybersecurity and regulatory compliance. By regularly testing and updating their incident response plans, organizations can ensure that they are prepared to respond to the ever-evolving threat landscape and minimize the impact of cyber incidents on their operations.
Compliance and Regulatory Requirements
As a manufacturer, ensuring compliance with relevant cybersecurity regulations and industry standards is crucial. Failure to adhere to these requirements can result in severe consequences, including hefty fines, legal liabilities, and damage to your company's reputation.
One of the most widely recognized cybersecurity frameworks is the National Institute of Standards and Technology (NIST) Cybersecurity Framework. This framework provides guidelines and best practices for managing and reducing cybersecurity risks across various industries, including manufacturing.
Another essential standard is the ISO/IEC 27001 Information Security Management System (ISMS). This standard outlines requirements for establishing, implementing, maintaining, and continually improving an information security management system within an organization. Compliance with ISO/IEC 27001 demonstrates your commitment to protecting sensitive information and maintaining a robust cybersecurity posture.
In addition to these general frameworks, there are industry-specific standards and regulations that manufacturers must comply with. For example, in the automotive industry, the UNECE Cybersecurity Regulation applies to all vehicles sold in the European Union. This regulation aims to ensure the cybersecurity of vehicles throughout their lifecycle, from design to decommissioning.
Similarly, the FDA's Cybersecurity Guidance for Medical Devices outlines recommendations for managing cybersecurity risks associated with medical devices, which are essential for manufacturers in the healthcare industry.
By adhering to these compliance and regulatory requirements, manufacturers can not only avoid penalties and legal consequences but also gain a competitive advantage by demonstrating their commitment to cybersecurity and earning the trust of customers and stakeholders.
Proconex's Cybersecurity Solutions
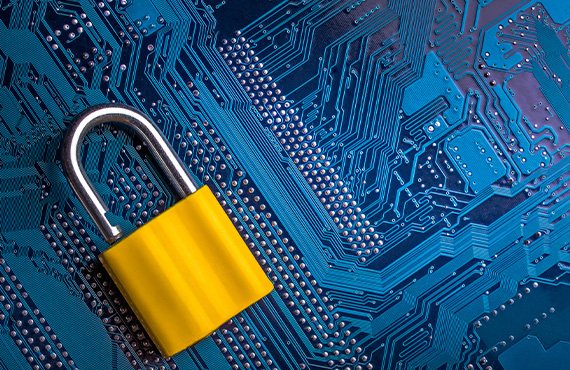
As a leading provider of industrial automation and cybersecurity solutions, Proconex offers a comprehensive range of services and expertise to help manufacturing companies address their cybersecurity challenges. Our team of highly skilled professionals possesses extensive knowledge and experience in implementing robust cybersecurity measures tailored to the unique requirements of the manufacturing industry.
Compliance with industry regulations and standards is a critical concern for manufacturing companies. Proconex offers compliance auditing services to assess your organization's adherence to relevant cybersecurity regulations and guidelines, such as NIST, IEC 62443, and industry-specific standards. Our experts provide recommendations and support to ensure your manufacturing operations remain compliant and aligned with best practices.
With our deep understanding of industrial control systems and operational technology environments, Proconex is well-equipped to address the unique cybersecurity challenges faced by manufacturing companies. Our solutions are designed to protect your critical assets, maintain operational continuity, and safeguard your valuable data and intellectual property.
Case Studies and Success Stories
Backup and Recovery for Mixed Controls Environment
A leading energy company required a comprehensive backup and recovery solution for their DeltaV distributed control system (DCS) environment as well as several non-DeltaV nodes and infrastructure components. Proconex designed and implemented a hybrid on-premises and off-site backup and recovery strategy, hosted from two separate management servers. This approach mitigated cybersecurity risks by eliminating unnecessary network bridges while supporting both DeltaV and non-DeltaV system nodes.
The DeltaV backup and recovery management server handled Emerson licenses and associated network nodes, while the non-DeltaV process-level management server managed non-Emerson-associated network nodes. Proconex developed a backup and recovery plan, detailed design specifications, and a disaster recovery plan with step-by-step instructions. The implementation and testing of the disaster recovery plan were also supported.
This energy customer received a successful, cost-effective solution tailored to their unique operating needs, streamlining their backup and recovery procedures while significantly reducing costs and simplifying management.
Staff Augmentation for Life Sciences Company
A prominent life sciences company required skilled resources for several months to help project manage and implement their global design standard. The technical requirement was for an ICS and cybersecurity engineer with deep expertise in current cybersecurity standards, policies, and rules, as well as strict adherence to procedures.
Proconex arranged for an engineering specialist to assist the customer on-site and remotely from its extensive team of OT cybersecurity experts. The expertise and close proximity of this resource proved invaluable in meeting the customer's unique scheduling requirements.
Benefiting from a significant presence in OT systems and a committed industrial cybersecurity unit, Proconex ensures the availability of a skilled technical workforce to guide customers at various stages of their operational journey.
Process Control Network and Asset Audit, and Recommendations
A large industrial company sought an independent provider with expertise in industrial controls, cybersecurity, and applicable standards to conduct a process control network and asset audit, and provide recommendations.
The customer desired a current and complete list of assets within the control network, an accurate OT network diagram, and professional resources to assess the risk and protection of the control networks.
Proconex conducted thorough site inspections, meticulously documented asset conditions, and offered comprehensive cybersecurity advisory services. The team deployed an on-site passive network monitoring tool to analyze and monitor OT network traffic.
During the assessments, Proconex scrutinized various site networks and their components, such as virtualized server setups, Microsoft configurations, switch and firewall settings, wireless network protocols, Active Directory Group Policies, network segmentation validations, identification of outdated hardware and software, DeltaV control system evaluations, remote access server examinations, and PLC network assessments.
Upon completion, the client received a detailed package of deliverables, including an asset inventory report, network connectivity diagrams, accurate network layouts showcasing data flows and device port details, a list of outdated equipment and software with suggested replacements, and consultations to address any highlighted high-risk areas discovered during the audit.
Segmentation for An Industrial Customer
An industrial customer had a flat network spanning their IT and OT domains, raising concerns about a cyber-attack penetrating their network perimeter and freely accessing other areas, processes, and systems.
Proconex initiated an evaluation and needs assessment before proceeding with a segmentation plan tailored to fulfill the unique requirements of the IT organization, DCS controls team, cybersecurity framework, labs, and executive priorities.
The solution development and execution included the selection and deployment of firewalls at strategic points within the newly established Intermediate Demilitarized Zone (IDMZ) at Layer 3.5. Stringent security policies were refined and updated for both IT and OT environments, with a focus on restricting traffic permissions to prevent unauthorized lateral movement by potential threats.
With this segmentation and other implemented risk mitigation strategies in their cybersecurity framework, the customer now operates with enhanced confidence. They have significantly reduced the likelihood of IT-related cyber threats infiltrating their OT network and vice versa. This proactive approach safeguards against potential disruptions such as loss of control, production delays, revenue impacts, quality metrics variance, and potential batch processing issues.
Key Takeaways
In today's interconnected world, cybersecurity is no longer an option but a necessity for manufacturing organizations. The increasing sophistication of cyber threats, combined with the potential consequences of a successful attack, make it imperative for manufacturers to prioritize cybersecurity measures.
Throughout this article, we have explored the importance of implementing a comprehensive cybersecurity strategy, securing industrial control systems, network segmentation and monitoring, incident response and recovery, and compliance with regulatory requirements. By adopting a proactive approach to cybersecurity, manufacturers can protect their operations, safeguard sensitive data, maintain business continuity, and enhance their overall competitiveness.
cybersecurity is an ongoing journey, and manufacturers must remain vigilant and continuously adapt to evolving threats. Regular risk assessments, employee training, and collaboration with trusted cybersecurity partners are crucial steps in building a resilient cybersecurity posture.
Remember, a single security breach can have devastating consequences, including financial losses, reputational damage, and operational disruptions. By prioritizing cybersecurity, manufacturers can mitigate these risks and ensure the long-term success and sustainability of their operations.
Proconex stands ready to assist manufacturing organizations in navigating the complex landscape of cybersecurity. With our expertise, industry-leading solutions, and proven track record, we can help you fortify your defenses, protect your assets, and maintain a secure and resilient manufacturing environment.
Frequently Asked Questions
Some of the most prevalent cyber threats in the manufacturing industry include malware attacks, phishing attempts, distributed denial-of-service (DDoS) attacks, and ransomware attacks. These threats can disrupt operations, compromise sensitive data, and result in significant financial losses.
Manufacturing companies rely heavily on industrial control systems (ICS) and operational technology (OT) to manage their production processes. A cyber attack on these systems can lead to production downtime, equipment damage, safety incidents, and even environmental disasters. cybersecurity measures are essential to protect these critical systems and ensure business continuity.
Manufacturing companies must comply with various cybersecurity regulations and standards, such as the NIST Cybersecurity Framework, ISO 27001, and industry-specific guidelines. This involves implementing robust cybersecurity measures, conducting regular risk assessments, and maintaining comprehensive documentation and audit trails.
A comprehensive cybersecurity strategy for manufacturing should include network segmentation, access controls, secure remote access, continuous monitoring, incident response planning, employee training and awareness, and regular risk assessments and audits. It should also incorporate best practices for securing industrial control systems and operational technology.
To protect industrial control systems, manufacturers should implement robust access controls, network segmentation, and secure remote access solutions. Regular software updates and patches should be applied, and security monitoring and incident response plans should be in place. In addition, employee training and awareness programs are crucial for identifying and mitigating cyber threats.