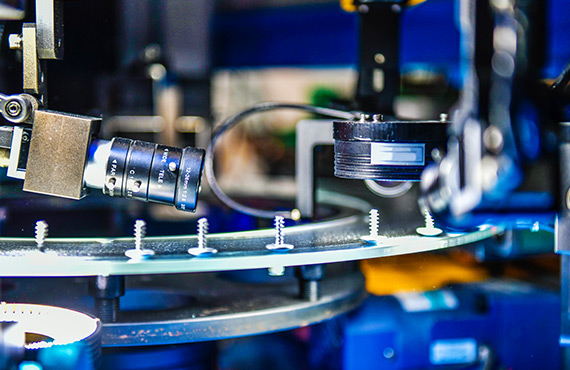
Smart process control systems use advanced automation technologies.
They gather real-time data from sensors, instruments, and equipment across industrial facilities. These systems surpass traditional process control. They do this by offering valuable insights through data analytics.
By implementing smart process control, you can reap many benefits, including the following:
- Meet complete visibility into all operations and processes.
- Identify issues before they cause downtime.
- Enhance quality control through continuous monitoring.
- Optimize assets and resources for maximum efficiency.
- Reduce waste and cut energy costs.
- Improve agility and ease decision-making.
- Boost equipment effectiveness (OEE).
- Prolong the lifespan of equipment.
- Empower teams with actionable data analytics.
- Maintain a safe working environment.
Smart process control systems enable real-time decision-making to drive tangible results. They do this by comprehending plant floor operations and processes.
Keep reading. You will learn more about the main features of these data-driven automation solutions.
Advanced Analytics
Smart process control systems use advanced analytics software and algorithms. They analyze collected data. They identify patterns and anomalies. This lets you pinpoint inefficiencies and problem areas in their operations.
Ensuring quick corrective action, alerts generate for abnormalities that need intervention. The analytics engines can predict future failures and demand changes. Over time, the algorithms fine-tune processes.
Automated process control uses machine learning to optimize control systems. These systems manage plant operations in real time. Industrial control systems collect data from sensors. They analyze it to improve process control.
But, connectivity exposes operations technology to cyber threats. Organizations must secure their OT and ICS. They need solutions tailored for industrial environments. Legacy systems lack modern security. But upgrades can disrupt critical processes.
Thus, a balanced approach is necessary. One that hardens defenses while enabling digitalization. With care, automated systems can stay resilient. Even as technology transforms.
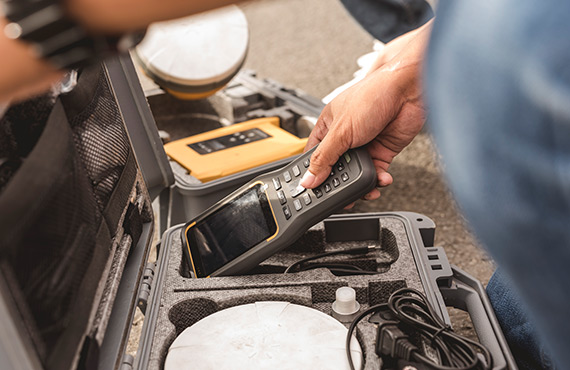
Maintenance
Smart process control systems enable predictive maintenance. They detect issues before equipment failure. These systems gather real-time data on various metrics. These metrics include vibration, temperature, pressure, and flow rates.
Through advanced analytics software, you can identify abnormalities and changes in baseline patterns. As a result, you can schedule proactive maintenance. This prevents unplanned downtime and costly repairs.
The advantages of predictive maintenance are significant:
- Service equipment before degradation occurs, resulting in increased uptime and reliability.
- Reduced maintenance costs: Planned repairs are much more cost-effective compared to emergency fixes.
- Improved worker safety: Preventing failures eliminates the risks of reactive work.
Smart process control systems can predict failures. Maintenance teams are aware of which assets need attention. They can take proactive measures to address potential problems.
This shift changes the maintenance approach from reactive to proactive.
Optimize Operations
Smart process control systems analyze operational data. They use algorithms to enhance processes for optimal efficiency.
The process control system acts as a digital brain. Instead of relying on manual supervision by operators. It makes small adjustments to reduce energy consumption. It also cuts waste, improves quality, and increases throughput. This real-time optimization results in efficiency improvements.
You can then adjust current processes to match past optimized scenarios.
Why?
Well, this eliminates the need for guesswork and ensures sustainable productivity optimization.
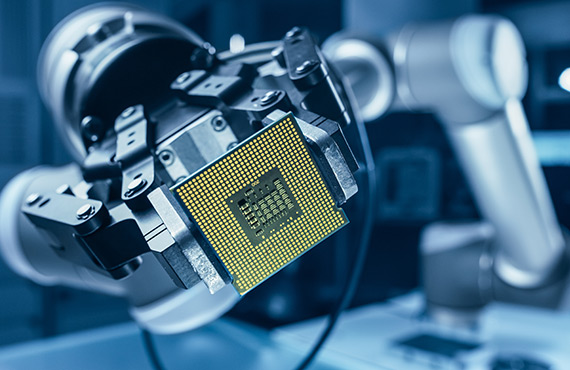
Reduce Downtime
Smart process control systems can decrease unexpected downtime. They also help you recover more when outages do happen.
When you track equipment health in real time, you can identify potential issues before they become critical. Then, you can schedule maintenance at optimal times. This helps you avoid unplanned stoppages.If outages do occur, automated diagnostics and analytics pinpoint the root cause. This lets maintenance teams resolve problems faster.
Some key advantages of smart process control systems include:
- Advanced pattern recognition can detect subtle performance changes. It can predict failures before they occur. This prevents surprise outages.
- Teams can intervene before minor problems escalate into major issues. Continuous monitoring provides instant notifications when thresholds are exceeded.
- Automated diagnostics analyze sensor data to identify the root causes of problems. This eliminates the need for lengthy manual troubleshooting processes.
- The ability to optimize maintenance around production schedules, minimizing disruptions.
Enhanced Quality Control
Smart process control systems enhance manufacturing quality. They detect defects and deviations from ideal parameters. Sensors gather data from all points on the production line. They measure temperature, pressure, flow rate, and vibration.
Automated alerts notify operators when fluctuations occur. This allows them to make necessary adjustments. It prevents the reaction from going out of specification. This proactive approach enables manufacturers to address potential quality issues. It also helps them avoid products failing to meet specifications.
As a result, you reduce waste and cost while increasing yields. Install smart systems to oversee critical parameters. This can ensure consistent quality output and cut disruptions caused by variability.
Improve Safety
Smart process control systems are essential for enhancing safety in industrial facilities. They also prevent hazardous conditions. These systems offer real-time insights into critical parameters. This enables the detection of abnormalities. It also allows the prompt sending of alerts before any dangerous situations arise.
You can automate your equipment to slow down or shut down. This happens if pressure, temperature, or vibration levels reach unsafe zones. This eliminates the need for human intervention and reduces the risk of accidents.
Further, these systems provide a constant stream of data. It lets facilities identify potential safety issues in advance. We use analytics to detect patterns. You can then address equipment problems or failures before they occur. Hence, you cut the chances of dangerous malfunctions.
Cost Savings
- Reduce maintenance costs. This proactive approach helps identify issues before they lead to failures. It minimizes unplanned downtime and expensive emergency repairs.
- Decrease energy usage. Smart systems can analyze demand patterns. They can then adjust energy inputs to ensure efficient energy consumption.
- Tight control over process parameters results in fewer quality problems and less waste. This mitigates the need for costly rework and scrap, saving manufacturers money.
- Identifying and eliminating bottlenecks and slowdowns improves throughput and yield. Optimized processes enable higher production volumes, increasing efficiency.
- Well-managed operations extend the lifetime of equipment by reducing wear and tear. Avoiding peaks in usage helps prolong the longevity of assets.
- Smoothing production flow through better planning and staffing reduces inventory and labor costs. Analyzing trends allows manufacturers to optimize resource allocation.
- Complete data records provided by smart automation systems help lower compliance costs. You can prove regulatory compliance, avoiding penalties and fines.
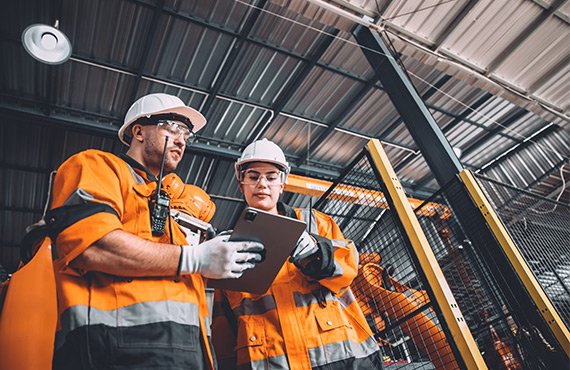
In Summary: Leverage Smart Process Control Systems for Operational Excellence
Process control systems have advanced, going above and beyond automation.
Today's solutions provide real-time data collection, advanced analytics, predictive maintenance, and more.
These capabilities optimize operations, reduce costs, and mitigate risks.
By adopting modern process control systems, you can enjoy:
- Improved visibility into all processes and assets.
- Early detection of issues to prevent downtime.
- Just-in-time maintenance based on predictive analytics.
- Tighter quality control through automated alerts and shutdowns.
- Safer operations with instant incident analysis.
- Lower operating expenses through energy savings and waste reduction.
To unlock these powerful advantages, partner with industry leaders like Proconex.
Contact Proconex today. Discover how smart process control systems can provide real-time insights.