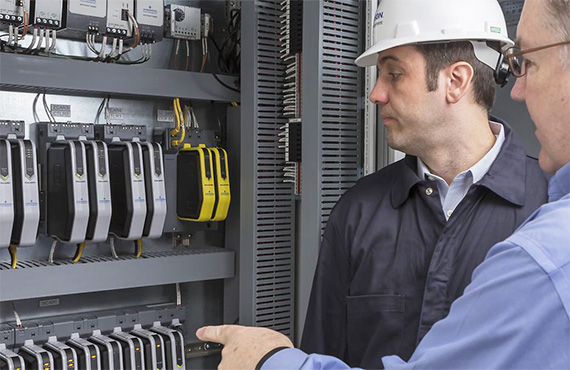
Looking to streamline your industrial operations and boost efficiency? You’re in the right place! At Proconex, we’re passionate about revolutionizing process automation through cutting-edge technology like distributed control systems (DCS).
These systems are game changers for industries aiming to simplify complex operations and enhance productivity. Let’s dive into how a distributed control system can elevate your facility; explore the differences between DCS and SCADA; and discover why Emerson DeltaV systems lead the pack.
What is a Distributed Control System?
A distributed control system empowers you to monitor and manage intricate industrial processes with ease. Picture a network of computers and controllers spread across your facility, all communicating seamlessly via a high-speed network. This setup allows you to collect real-time data from sensors and send precise control signals to actuators, ensuring smooth operation of variables like temperature, pressure, and flow. Whether you’re running an oil refinery, power plant, or chemical facility, a DCS system provides intelligent control that’s simple to operate and maintain; it’s designed to handle multi-component automation while keeping your processes safe and efficient.
Distributed Control System vs. SCADA
You might wonder how a DCS control system differs from SCADA (Supervisory Control and Data Acquisition). While both systems manage industrial processes, they serve distinct purposes. A DCS distributed control system excels in localized, complex process control; it integrates all control functions into a single, cohesive system, making it ideal for continuous manufacturing like pharmaceuticals or oil refining. SCADA, on the other hand, focuses on supervisory monitoring across geographically dispersed assets, often used in industries like water distribution or power grids. With a distributed control system, you gain modular, scalable control capabilities; SCADA offers broader oversight but less depth in localized process management.
When you choose a DCS system, you’re opting for a solution that prioritizes real-time, high-speed control within a single facility. It’s built to handle thousands of I/O points with precision, ensuring every valve, pump, and sensor operates in harmony. SCADA systems, while powerful for remote monitoring, often rely on slower communication protocols like radio or satellite, which can introduce latency; they’re better suited for collecting data from distant sites and providing high-level oversight rather than granular control.
Additionally, a DCS offers advanced diagnostic tools and redundancy features, minimizing downtime in critical operations. SCADA, while capable of alarming and trending, often lacks the same level of fault tolerance and integration depth. If your operation demands tight control loops and seamless automation, a DCS automation solution is your best bet; for wide-area monitoring with less focus on real-time control, SCADA might be the better fit. Understanding your operational needs will guide you to the right system for your facility.
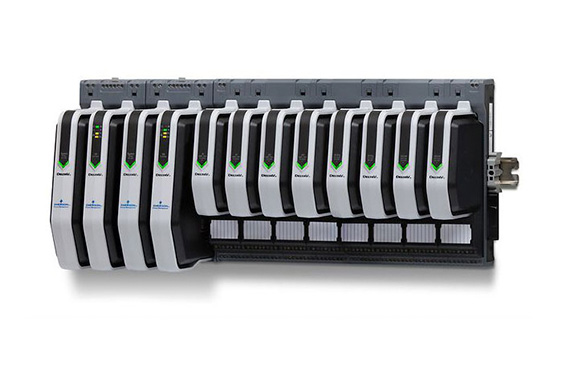
Emerson DeltaV™ Systems: Powering Your Operations
At Proconex, we proudly offer the Emerson DeltaV™ distributed control system, a leader in DCS automation. Emerson combines ease of use, full-scale control, and powerful integration to simplify your operations and boost productivity. The DeltaV™ DCS leverages predictive technologies in an intuitive, interoperable way; it’s built to increase plant performance, adapt to your needs, and lower project risks and costs. You can easily access real-time, secure, contextualized data to drive operational improvements; plus, DeltaV™ Version 15 offers ultimate scalability and enhanced performance to meet your future needs.
Our selection of DeltaV™ products includes high-performance controllers with embedded advanced control functions; a wide variety of I/O modules (analog, digital, and special-purpose); and intuitive engineering tools for configuration, programming, and diagnostics. Whether you’re managing a small skid unit or a large distributed process plant, the DeltaV™ PK Controller delivers a feature-packed solution; it supports standard communication protocols like OPC, Modbus, and Profibus for robust connectivity. Ready to transform your operations? Explore our distributed control systems and see how Emerson DeltaV™ can elevate your facility today.
Key Takeaways
Here’s what you need to know about distributed control systems and their impact on process automation:
- A DCS system provides centralized, real-time control for complex industrial processes; it’s perfect for industries like oil, gas, and pharmaceuticals.
- Unlike SCADA, which focuses on remote monitoring, a DCS distributed control system excels in localized, high-speed automation with advanced diagnostics and redundancy.
- The Emerson DeltaV distributed control system offers scalability, predictive technology, and seamless integration; it’s designed to enhance plant performance and reduce operational risks.
- With a DCS control system, you can manage thousands of I/O points with precision; this ensures operational efficiency and safety in your facility.
Frequently Asked Questions
A distributed control system shines in industries like oil and gas, chemical manufacturing, power generation, and pharmaceuticals; these sectors rely on continuous, complex processes that demand precise, real-time control.
Yes, modern DCS systems like Emerson DeltaV support standard protocols such as OPC and Modbus; this ensures seamless integration with your existing equipment and systems.
A DCS control system centralizes control, reduces manual intervention, and provides real-time data for better decision-making; it also minimizes downtime with built-in redundancy and diagnostics.
The Emerson DeltaV distributed control system offers unmatched scalability, predictive technology, and user-friendly interfaces; it’s designed to adapt to your needs while enhancing plant performance and safety.